Celikform Gestamp launches hinge production four spindle machining center from LiCON
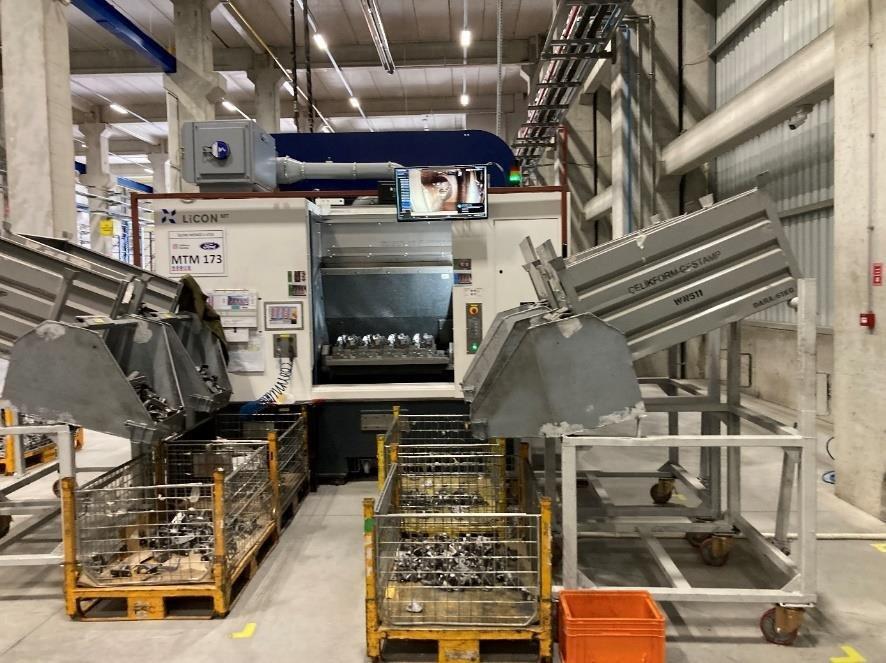
Kathmandu Nepal
Dienstag, Apr. 22, 2025
Three strong points
Milestone project
Mustafa Ugur Alayci, explains the decision for the LiCON machines: "The LiCON four-spindle LiFLEX IV 244 DL DT B00 convinced us. With four spindles working parallel on each machine, only two machines were required for the entire volume." As Business Development Manager at Celikform, he drove this project for Celikform. It was a milestone project for Celikform. Coming from the sheet metal fabrication, the machining was an additional process, opening doors for further business. Besides the machining centers, all the peripheries had to be installed, such as CMM and tool set-up rooms.
With all these challenges ahead, LiCON was chosen as partner. Celikform selected sixty years of experience. "These machines are robust and strong, with approx. 18% more spindle torque than the alternatives," explains Fatih Acet, the Production Technologies Manager.
Maximum production on minimum floor space
Each four-spindle machine has two bridges on the double trunnion, which allows loading parallel to machining. Eight different part numbers are loaded to the bridges of the two machines. No manual changeover is required. With each cycle of the two machines, four passenger cars can be equipped with the door hinges. The smart design of the clamping fixture allows for a compact arrangement.
The LiCON department designs, builds and tests clamping fixtures inhouse. Many customers appreciate the turn-key solutions from one hand. LiCON supplied the machine fit for the process, i.e. with fixtures, tooling and process run-off.
With a floor space of only 50 m² including the manual loading area, the four-spindle machines use almost no space relative to the high production volumes.
Energy saving
Energy saving becomes more and more important. Both machines are equipped with minimum quantity lubrication (MQL) in lieu of the traditional coolant. This technology is known for two decades now and more and more producers take advantage of up to 40% energy saving and longer tool live.
Successful project
All the challenges were mastered, and new standards set in the production of passenger car hinges. Celikform is now recognized as a reliable supplier for such parts by leading car manufacturers. " With LiCON, we have found the right partner for the machining" says Semih Kurt, Purchasing Manager.
About Çelikform Otomotiv A.Ş.
Çelikform Gestamp manufactures process and new generation materials with cutting-edge technology, along with body and mechanism parts in its production area in TEKNOSAB for automotive key industry.
LiCON mt GmbH & Co. KG, a global system supplier of modular machining centers stands for high-precision machining in series production. Core products are horizontal machining centers, with single-spindle, twin-spindle and even four-spindles. Unique is the portfolio of loading options. LiCON offers all three options, direct loading, double trunnion and pallet changer. Most of its customers from the automotive and other industries, appreciate the technology expertise and select a turnkey solution including the machining process. LiCON is dedicated to keep the quality of the machine and the machining process under control. That is why LiCON develops, designs and builds fixtures, motor spindles and most of its machine components inhouse.
Additionally, system integration with customized adaptable automation concepts.
With 200 employees in Europe, US, and China, LiCON is perfectly sized to lead in technology and be a flexible partner to its customers worldwide.
More information: www.licon.com
Licon mt GmbH & Co. KG
Im Rißtal 1
88471 Laupheim
Telefon: +49 (7392) 962-0
Telefax: +49 (7392) 962-257
http://www.licon.com