Navigating the Hazards of Steelmaking: Ensuring Safety in the Process
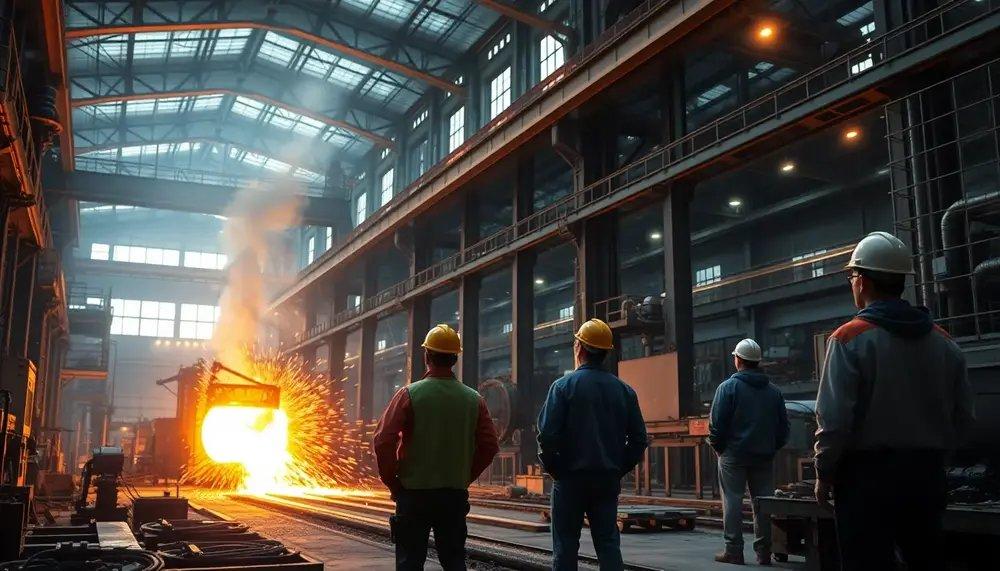
Breaking News:
Kathmandu Nepal
Sonntag, Juli 6, 2025
Introduction to Steelmaking Hazards
Steelmaking, it’s quite the beast, isn’t it? This industry, while vital, comes with its own set of challenges. From the roar of machinery to the intense heat, every corner seems to hide a potential danger. But, don’t let that scare you off. Understanding these hazards is the first step to conquering them. Think of it as a puzzle; once you know the pieces, you can fit them together safely.
So, what are we really dealing with here? It’s not just about big machines and hot metal. There’s a whole range of risks that workers face daily. It’s like walking a tightrope, balancing efficiency with safety. And while it might sound daunting, it’s also an opportunity. An opportunity to innovate, to improve, and to make steelmaking not just productive, but safe for everyone involved.
Let’s dive into this world, shall we? We’ll explore the specific hazards lurking in the steelmaking process and how we can navigate them. It’s all about being prepared and proactive. After all, knowledge is power, especially when it comes to keeping people safe.
Understanding Machinery Risks in Steel Production
Machinery in steel production, well, it’s a bit like a double-edged sword. On one hand, these massive machines are the backbone of the industry, driving efficiency and production. On the other, they can be downright dangerous if not handled with care. So, what’s the scoop on these machinery risks?
First off, let’s talk about moving parts. You know, those gears, belts, and rollers that seem to have a mind of their own. They can catch clothing, fingers, or anything else that gets too close. It’s crucial to keep your wits about you and always follow safety protocols. Lockout/tagout procedures are your best friends here, ensuring machines are properly shut down before maintenance.
Then there’s the issue of maintenance itself. Regular checks and servicing are non-negotiable. Think of it like a car; you wouldn’t drive it for years without an oil change, right? The same goes for these machines. Regular maintenance keeps them running smoothly and safely.
Lastly, let’s not forget about the noise. It’s not just an annoyance; it can be a hazard. Prolonged exposure to loud machinery can lead to hearing loss. So, always wear your ear protection and be mindful of your surroundings.
In a nutshell, understanding machinery risks is all about respect. Respect for the power of these machines and respect for the safety measures in place. With the right approach, these risks can be managed effectively, keeping everyone safe and sound.
Preventing Falls and Managing Heights
Working at heights in the steel industry is like walking on a high wire. It’s thrilling, sure, but one misstep can lead to a nasty fall. So, how do we keep our feet firmly on the ground, metaphorically speaking?
First up, let’s chat about equipment. Harnesses, guardrails, and safety nets are your best pals when you’re up high. They might not be the most comfortable gear, but they sure do save lives. It’s all about having the right tools for the job and knowing how to use them.
Next, training is key. You wouldn’t climb a mountain without knowing how to use your climbing gear, right? The same goes for working at heights. Proper training ensures that workers know the risks and how to mitigate them. It’s not just about knowing what to do; it’s about knowing why it matters.
Let’s not forget about the buddy system. Having a colleague nearby can make all the difference. Whether it’s spotting potential hazards or lending a hand, teamwork is essential. After all, two heads are better than one.
Lastly, maintaining a tidy workspace is crucial. Clutter can lead to trips and falls, so keeping things organized is a must. It’s a simple step, but it goes a long way in preventing accidents.
In essence, preventing falls and managing heights is all about preparation and vigilance. With the right mindset and tools, we can keep our feet on solid ground, even when we’re up in the air.
Protecting Against Falling Objects
In the bustling environment of a steel plant, the risk of falling objects is as real as it gets. Imagine tools, debris, or even small parts taking a dive from above. Not a pretty picture, right? So, how do we keep our heads safe and sound?
First things first, let’s talk about headgear. Hard hats are a staple for a reason. They might not win any fashion awards, but they’re a crucial line of defense against falling objects. It’s like having an umbrella in a rainstorm—essential and lifesaving.
Next, securing tools and equipment is a no-brainer. Using tool lanyards and storage solutions can prevent items from becoming airborne hazards. It’s all about keeping things in their place, so they don’t end up where they shouldn’t be.
Signage plays a big role too. Clear signs indicating areas where overhead work is happening can alert workers to be extra cautious. It’s a simple way to communicate potential risks and keep everyone on their toes.
Finally, regular inspections of overhead structures can catch potential issues before they become problems. It’s like checking the roof for leaks before the rainy season hits. Proactive measures can save a lot of headaches—literally.
In short, protecting against falling objects is about being aware and taking preventive steps. With the right precautions, we can keep the sky from falling, at least in the steel plant.
Mitigating Traffic Accident Risks in Steel Facilities
In the fast-paced world of steel facilities, traffic accidents can be a real headache. With forklifts zipping around and heavy trucks on the move, it’s like a bustling city street. So, how do we keep the chaos in check?
First, let’s lay down the law with clear traffic rules. Designated lanes for vehicles and pedestrians can prevent a lot of close calls. It’s like having lanes on a highway—everyone knows where they should be, reducing the chance of collisions.
Next up, training drivers is crucial. Ensuring that everyone operating a vehicle knows the ins and outs of safe driving practices is key. It’s not just about knowing how to drive; it’s about understanding the unique challenges of a steel facility environment.
Signage and signals are your best allies here. Clear signs and signals can guide traffic and alert drivers to potential hazards. Think of them as the traffic lights and stop signs of the plant, keeping everything flowing smoothly.
Regular maintenance of vehicles is another must. Just like you wouldn’t drive a car with faulty brakes, the same goes for industrial vehicles. Keeping them in top shape prevents mechanical failures that could lead to accidents.
Finally, fostering a culture of awareness and communication can make a world of difference. Encouraging workers to stay alert and communicate any issues can help nip potential problems in the bud.
In essence, mitigating traffic accident risks is all about structure and vigilance. With the right systems in place, we can keep the wheels turning safely and efficiently.
Addressing Process Risks: Heat and Hazardous Substances
When it comes to steelmaking, the heat is on—literally. The process involves extreme temperatures and hazardous substances that can pose significant risks. So, how do we keep things cool and safe?
First, let’s tackle the heat. Personal protective equipment (PPE) like heat-resistant gloves and suits are essential. They act as a barrier between workers and the intense temperatures, allowing them to handle hot materials without getting burned.
Ventilation systems also play a crucial role. Proper airflow can help dissipate heat and reduce the risk of heat-related illnesses. It’s like having a breeze on a hot day, making the environment more bearable and safe.
Now, onto hazardous substances. Handling chemicals and other dangerous materials requires a cautious approach. Safety data sheets (SDS) provide vital information on how to manage these substances safely. It’s like having a manual that tells you exactly what to do in case of a spill or exposure.
Training is, once again, a key player. Workers need to know how to handle these substances properly and what to do in case of an emergency. It’s about being prepared and knowing the drill.
Lastly, regular monitoring and maintenance of equipment can prevent leaks and spills. Keeping everything in check ensures that hazardous substances stay where they belong—safely contained.
In summary, addressing process risks in steelmaking is about preparation and protection. With the right measures in place, we can keep the heat and hazards at bay, ensuring a safe working environment for all.
Implementing Effective Safety Measures
Creating a safe environment in steelmaking isn’t just about ticking boxes; it’s about crafting a culture where safety is second nature. So, how do we make safety measures stick?
First, let’s focus on training. It’s not a one-and-done deal. Regular, engaging training sessions keep safety top of mind. Think of it as sharpening a tool—constant attention keeps it effective. And hey, why not make it interactive? Quizzes, simulations, and real-life scenarios can make learning about safety more engaging and memorable.
Next, communication is key. Open lines of communication ensure that everyone is on the same page. Regular meetings and updates about safety protocols keep everyone informed. It’s like having a team huddle before the big game—everyone knows the plan and their role in it.
Then there’s the importance of feedback. Encouraging workers to speak up about potential hazards or improvements can lead to valuable insights. After all, those on the front lines often have the best perspective on what works and what doesn’t.
Regular audits and inspections are also crucial. They help identify areas for improvement and ensure that safety measures are being followed. It’s like having a checklist to keep everything in order, ensuring nothing slips through the cracks.
Finally, let’s not forget about recognition. Acknowledging and rewarding safe behavior can motivate others to follow suit. It’s a simple way to reinforce the importance of safety and encourage a proactive approach.
In essence, implementing effective safety measures is about building a community where safety is everyone’s responsibility. With the right approach, we can create a workplace where safety isn’t just a priority—it’s a way of life.
Case Study: Success in Reducing Hazards
Let’s dive into a real-world example of how one steel plant turned things around and made safety a shining star. This case study is all about innovation, teamwork, and a dash of creativity.
At SteelCo, a mid-sized steel manufacturer, they were facing a spike in workplace incidents. The management knew something had to change, so they decided to take a bold approach. Here’s what they did:
The results? A remarkable 40% reduction in workplace incidents within a year. The atmosphere at SteelCo transformed, with safety becoming a core part of their culture. Workers felt valued and empowered, knowing their voices were heard and their safety was a priority.
This case study shows that with a bit of creativity and a lot of collaboration, reducing hazards in steelmaking is not just possible—it’s achievable. SteelCo’s journey is a testament to the power of proactive safety measures and the impact they can have on a workplace.
Utilizing OSHA Resources and Guidelines
When it comes to safety in steelmaking, the Occupational Safety and Health Administration (OSHA) is like a trusty compass guiding the way. Their resources and guidelines are invaluable tools for navigating the complex landscape of workplace safety.
First off, OSHA provides a treasure trove of guidelines tailored specifically for the steel industry. These aren’t just generic rules; they’re crafted with the unique challenges of steelmaking in mind. By aligning your safety protocols with OSHA’s standards, you’re not just complying with regulations—you’re setting a high bar for safety excellence.
One of the standout resources is OSHA’s online database. It’s packed with information on everything from hazard communication to emergency response. Whether you’re looking for detailed regulations or practical tips, it’s all there at your fingertips. Think of it as a library dedicated to keeping workers safe.
OSHA also offers training programs that can be a game-changer for your team. These programs are designed to educate workers on best practices and equip them with the knowledge they need to stay safe. Plus, they’re a great way to ensure everyone is on the same page when it comes to safety protocols.
And let’s not forget about the consultation services. OSHA provides free, confidential consultations to help identify potential hazards and improve safety measures. It’s like having a safety expert on speed dial, ready to offer guidance and support.
In short, utilizing OSHA resources and guidelines is about tapping into a wealth of knowledge and expertise. By doing so, you’re not just enhancing safety—you’re fostering a culture where safety is woven into the fabric of your operations. With OSHA by your side, you’re well-equipped to tackle the challenges of steelmaking and create a safer workplace for everyone.
Conclusion: Prioritizing Safety in Steelmaking
In the grand scheme of steelmaking, safety isn’t just a checkbox—it’s the foundation upon which everything else is built. As we’ve journeyed through the various facets of ensuring safety, one thing is crystal clear: it’s a collective effort that requires constant attention and commitment.
From understanding the intricacies of machinery risks to implementing robust safety measures, every step is crucial. It’s about creating an environment where workers feel protected and valued, where their well-being is as important as the steel they produce. After all, a safe workplace is a productive workplace.
Utilizing resources like those from OSHA provides a solid framework, but it’s the human element—engagement, communication, and vigilance—that truly brings safety to life. By fostering a culture where safety is prioritized, we not only protect our workforce but also enhance the overall efficiency and reputation of the industry.
In conclusion, prioritizing safety in steelmaking is an ongoing journey. It’s about staying proactive, embracing innovation, and never losing sight of the ultimate goal: ensuring that every worker goes home safe and sound at the end of the day. With dedication and collaboration, we can navigate the hazards of steelmaking and pave the way for a safer, brighter future.
Die Provimedia GmbH ist ein Online-Verlag mit Sitz in der Region Stuttgart. Wir schaffen wertvolle Informationen in unterschiedlichen Branchen um Wissen schnell und einfach zugänglich zu machen. Wir haben uns auf übersichtliche Webseiten und Auffindbarkeit von Informationen spezialisiert.
Provimedia GmbH
Weidenweg 12
74321 Bietigheim-Bissingen
Telefon: +49 (7142) 3442727
Telefax: +49 (7142) 2279985
http://provimedia.de