BST system solutions for quality assurance make production of fuel cells and electrolyzers more efficient
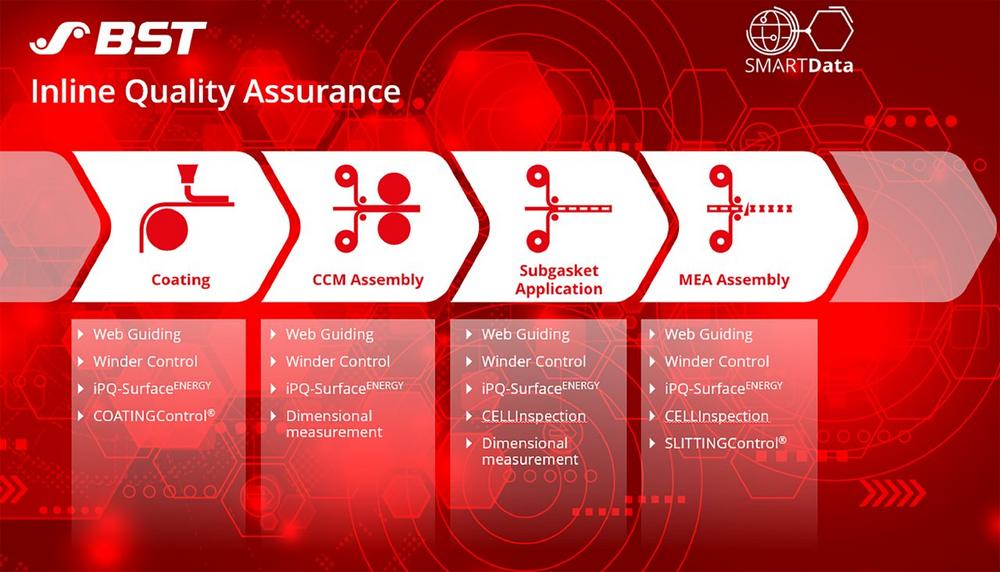
Breaking News:
Kathmandu Nepal
Dienstag, Apr. 22, 2025
Electrochemical energy converters, such as fuel cells and electrolyzers, will play a key role in a number of sectors in the future, especially in areas that rely on zero- or low-emission energy sources. Especially the transportation sector, stationary energy supply, heavy industry and logistics will benefit from the development and use of hydrogen technologies. BST acts as a direct partner to the battery and fuel cell industry and contributes with its highly efficient quality assurance systems to ensure that only 100% safe and reliable end products are produced.
BST system solutions help fuel cell industry take off
"The industry is in a state of upheaval," says Johannes Scholz, Technical Sales Manager at BST. "Many companies need to convert their machines from sheet-to-sheet production to much faster roll-to-roll production. The problem remains: Even the smallest irregularities in the coating or deviations in position can lead to unacceptable quality losses and therefore to waste". Competition is increasing, production costs need to be reduced, and there is a shortage of skilled labor. In the face of these challenges, there is a need for solutions that deliver competitive advantage through automation, efficiency and sustainability. BST’s high-precision quality assurance solutions can eliminate or greatly reduce inefficient inspection, unplanned machine downtime and the resulting delivery delays. They are also easy to use, with a clear user interface that does not require the operator to do much, making them less dependent on a shortage of skilled labour.
BST system solutions for the production of fuel cell components in line
Precise geometric measurement is a prerequisite for avoiding defects and ensuring optimum quality in all the web-forming production steps of a fuel cell. Inspection systems perform various measurement tasks in the production process, but can also transfer their measurement data to the web guiding systems. The BST CELLInspection for geometric measurement precisely measures the individual layers and coating positions up to the cutting edge inline during the production process. In case of deviations, automatic feedback can be given to the web guiding system. The perfect geometric positioning of the individual layers to an MEA is a key quality criterion.
The iPQ-Surface ENERGY high-end surface inspection system ensures quality across all process steps. It consists of high-resolution cameras, multiplexed illumination and a software architecture with numerous interfaces for easy integration into Industry 4.0 environments. Other features include AI-based defect classification and complete quality documentation, as well as a clear display of all measurement results and defects. The user interface of the iPQ-SurfaceENERGY surface inspection system clearly displays any relevant quality deviation, giving the user maximum control for error-free production of individual layers.
Quality assurance the smart way
Whether it is a question of quality assurance in the coating process, in the assembly process or in the assembly of individual components: BST offers different solutions for each step in the production of fuel cells, which can be adapted to the individual conditions of the machine environment. In addition to the BST CELLInspection and iPQ-Surface ENERGY inspection systems, this also includes the BST COATINGControl application solution for perfect positioning of the coating on the substrate, or web guiding systems such as FRAMEGuide Pro, which guarantees maximum precision with a repeatability of ±10 μm at minimum installation height, and others.
What all these solutions have in common is that they prevent quality defects. Not only do they detect defects, but they also prevent them from occurring by correcting faulty production processes. This is where SMARTData comes in: the central data management solution with open interfaces enables the integration of different web guiding and quality assurance systems, thus supporting a cross-process data exchange that is unique in the industry.
BST GmbH, a company of the elexis Group, is one of the leading suppliers of quality assurance systems for the web processing industry. The Bielefeld-based company offers solutions for web guiding, surface inspection, web monitoring, 100% inspection, color measurement, color management, register control and automation. The company has decades of practical experience in these areas, with installations at more than 15,000 customers worldwide in the printing and packaging, paper and film, rubber and tire, battery and fuel cell, and printed and organic electronics industries. BST stands for high-quality quality control, smooth production processes and first-class service worldwide. www.bst.elexis.group
elexis AG
Industriestr. 1
57482 Wenden
Telefon: +49 (2762) 612-130
Telefax: +49 (2762) 612-135
http://www.elexis.group