Measure energy consumption, avoid wear
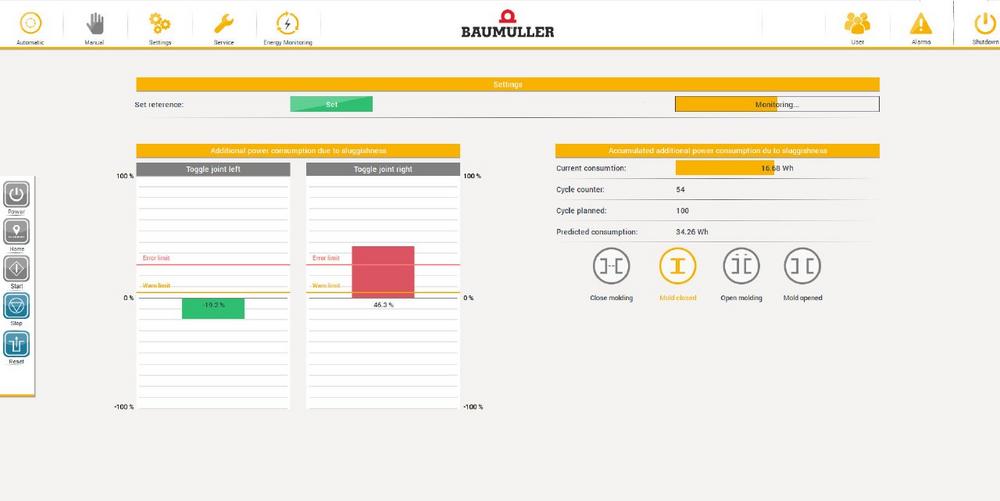
Breaking News:
Embedded Softwareentwicklung: Besonderheiten und Herausforderungen
Backorder und Catchen von Domains: Die Strategie zur Wunschdomain
World’s first full integration of IEC 61850 into plant engineering with Engineering Base
Weltweit erste Vollintegration der IEC 61850 ins Anlagen-Engineering mit Engineering Base
Kathmandu Nepal
Sonntag, März 16, 2025
With this function, the energy consumption of individual production orders can be transparently recorded and, in a second step, optimized on the basis of a reference value. The reference measurement also serves as an initial value for detecting energy deterioration in the production process. Warning and error thresholds can then be set up on the basis of these values.
The software is loaded directly into the servo-controller and is therefore easy to retrofit. Energy consumption is recorded directly via the intelligent drive. This saves additional costs for external sensors and reduces the amount of wiring required.
Transparency from each axis to the entire system
With the new function, the energy consumption of each individual axis can be determined per cycle. The energy measurement is performed autonomously and in real time in the Baumüller b maXX servo converters used. In the higher-level PLC function in the b maXX converter, a software module analyzes the transferred measured values and subsequently calculates, among other things, the actual energy consumption per axis as well as across all axes. The values are then shown in the machine visualization. Alternatively, a dashboard also displays the results of the measurement, which are directly transferred from the b maXX converter via open IoT interfaces, such as OPC UA.
For the machine manufacturer or end user, this function offers the following possibilities:
• Optimization of the machine cycle reduces the energy consumption of the machine and accordingly of individual energy consumers within the machine Lower production/energy costs during operation
• Optimization of the machine cycle regarding the use of energy in the DC link Lower production/energy costs during operation
• Representation of energy consumption per part Facilitates and improves the calculation of production costs
• Energy deterioration (e.g. increasing mechanical wear) is automatically detected on the basis of adjustable warning and error thresholds Maintenance for increased machine availability can be planned and carried out in a cost-optimized way
• Interfaces to comprehensive energy measurement systems possible Transparency of the entire machine’s energy consumption
• Machine-specific key figures can be generated Improved process optimization, including monitoring
• Transparency of energy consumption Assists in the determination of the Product Carbon Footprint (PCF)
Software functions
The Smart Energy Monitoring software function can be applied in the softdrivePLC of the Baumüller converter and operated via a higher-level control unit. This control unit is manufacturer-independent. The module in the Baumüller control unit works with the current energy values from the converters, generates a reference, and can compare subsequent cycles with this reference using defined threshold values. In addition to the relative changes to the reference, the actual values can be displayed in a visualization.
The following parameters are calculated:
• Predicted energy consumption per cycle
• Actual energy consumption of the drive per cycle
• Actual energy consumption of the drive per order
• Comparison of the predicted and the actual energy consumption
Process optimization based on regenerative effects
To support production in optimizing the machine cycle, the software calculates the regenerative effect, also referred to as the “green factor.” This provides information about the potential for process optimization. This key figure can be improved by ensuring that the process makes more optimal use of the energy regenerated in the braking process. For example, after braking one axis, another axis can be accelerated again with the DC link energy. These measurement methods help machine operators to perform their production processes with the highest possible energy efficiency.
Preventive machine protection through comparison routine
The new software function continuously measures and adjusts the machine’s power consumption. If the energy balance deteriorates and higher average values are output, further analysis can be carried out on this basis. Any wear or need for maintenance can thereby be detected immediately. This can prevent both an increase in energy costs and unplanned maintenance work and breakdown times, improving machine availability at the same time. The threshold values for error and warning messages can be set individually.
Based in Nuremberg, Baumüller is a leading manufacturer of electric automation and drive systems. At production sites in Germany, the Czech Republic, Slovenia, and China as well as in over 40 branches worldwide, around 2,000 employees develop and produce intelligent system solutions for machine manufacturing and e-mobility.
In addition, the range of services offered by the Baumüller Group includes engineering, assembly, and industrial relocation as well as services, thus covering all aspects of life cycle management.
Baumüller Gruppe
Ostendstraße 80-90
90482 Nürnberg
Telefon: +49 (911) 5432-0
Telefax: +49 (911) 5432-130
http://www.baumueller.com