High performance in robot welding with the new LMR 2 torch generation by Lorch
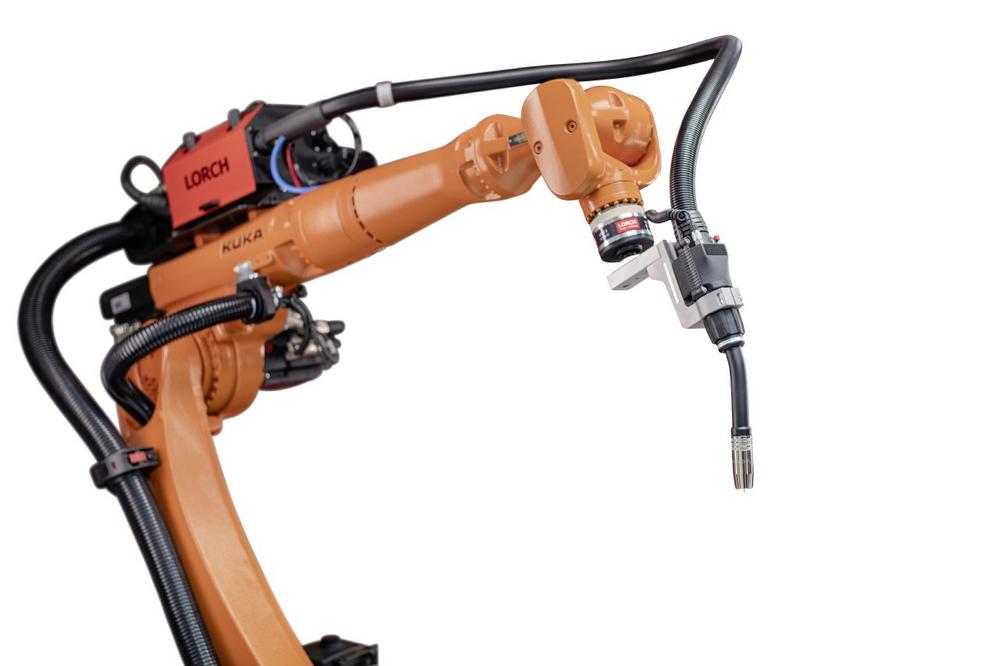
Breaking News:
Kathmandu Nepal
Freitag, Nov 15, 2024
Long duty cycles, enormous precision in the repeat rates, fast material throughput: robot welding poses particularly high demands to welding. With the new LMR 2 torch generation, available for all common robot types, Lorch Schweißtechnik is offering a welding system that represents highest quality and reproducibility. The LMR torch offers outstanding performance and productivity thanks to a number of innovations that have already been implemented with the new LMS hand-held torch system. The reason for this is the specially designed torch interior: The coordinated shapes of the contact tip and contact tip holder makes the gas flow laminar to ensure perfect gas coverage. The drawn contact tip counteracts the formation of micro arcs in the inner contact tip while the special design adds a wire straightening effect and optimises current transfer to the wire. The highly stable arc and improved material transition make weld seams more precise. Temper colours when welding stainless steel are minimised as well, and fume and soot are also reduced when welding aluminium.
The special design of the brass tip adapter/gas diffuser allows quick heat discharge and protects from too-high thermal stress at long runtimes. The innovative shielding gas routing provides additional cooling of the contact tips and optimises gas flow at the front end of the torch. Consistent implementation of copper-copper connections and highly efficient cooling clearly reduce the overall resistance in the torch. Both greatly protect the installed wear part components and increase their service lives.
Not only the innovative cooling system that clearly reduces wear protects resources, but so does the gas-saving, separate shielding gas routing and the repair-friendly design, both of which help increase sustainability. The hose packages and their connections to the torch can be replaced easily and the wear parts in the LMR torch are mostly identical with those in the LMS torches from manual welding. This reduces warehousing of wear parts if robot systems and manual welding systems are both used in the same company.
The LMR 2 torches are available in two versions – TN 3 and TN 6. The TN 3 torch is equipped with a long torch neck and particularly suitable for production processes where good access to the weld seams is important, e.g., when welding thin sheets in the automotive industry. The power range of the TN 3 goes from 300 to 450 amperes, depending on cooling (water, gas). The high-end torch TN 6 with its shorter torch neck is designed for higher currents of 300 to 500 amperes. All in all, 16 different performance packages can be selected as complete solutions, depending on robot concept, wire feed option, cooling method, and torch version.
The LMR 2 torches can be combined with any common robot system and the Lorch S-RoboMIG XT and Robo-MicorMIG power sources. The power sources make the tried and tested SpeedPulse XT, TwinPuls XT, SpeedArc, SpeedArc XT, Pulse, and TwinPuls Lorch welding processes, which are in high demand, available for robot welding.
Heiko Hedderoth, product manager at Lorch: “The LMR 2 torches by Lorch once again clearly increase power and economic efficiency in robot welding. They represent high performance, high precision, and longevity. The further components give customers and optimal welding package for their robot from a single source. The precisely coordinated components optimise welding results for all materials, be they aluminium, steel, or stainless steel. They are available for applications in many different industries.”
Lorch Schweißtechnik GmbH is a leading manufacturer of arc welding systems for industrial applications, the demanding metal craft, as well as for use in the automation with robots and collaborative robot systems. In-house developed helmet and torch systems add to ensuring optimal welding results. Lorch high-quality systems have been produced in one of the world’s most state-of-the-art welding system productions in Germany and exported into more than 60 countries for more than 65 years. Welding technology by Lorch combines great practical benefits, very simple operation, and high economic efficiency, setting new technology standards on the market.
Lorch Schweisstechnik GmbH
Im Anwänder 24-26
71549 Auenwald-Mittelbrüden
Telefon: +49 (7191) 503-0
Telefax: +49 (7191) 503-199
http://www.lorch.eu