End-to-End Mineral Processing Testwork Successfully Completed on Taronga Tin Project Bulk Sample
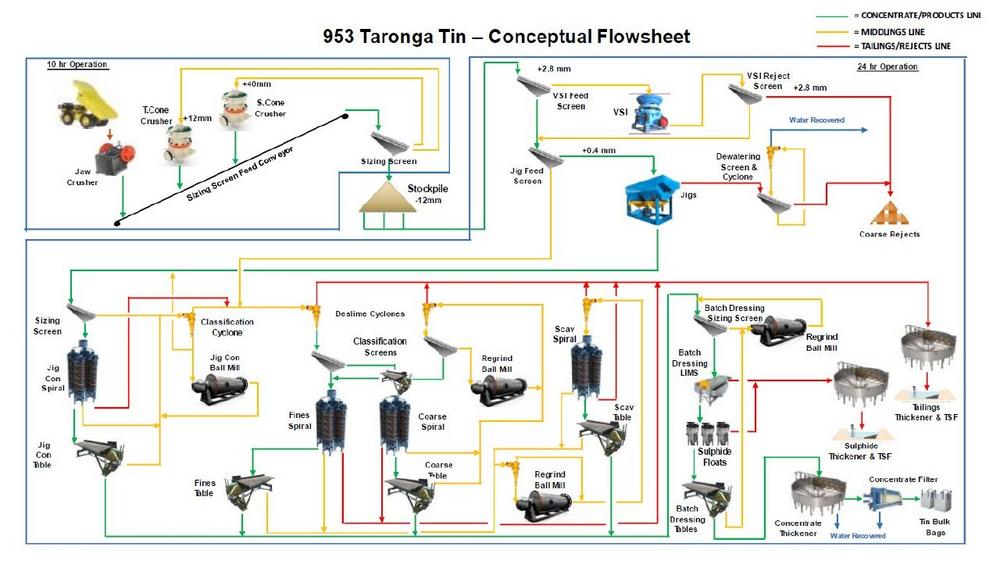
As recently reported, previous crush, jig and spiral test results confirmed the premise that the cassiterite (SnO2 – tin ore mineral) is easily liberated at a coarse crush size and that a good quality pre-concentrate can be obtained using very simple gravity separation techniques.
Using coarse gravity techniques only (i.e. no fine tin recovery) and a processing route that consists only of crushing, jigs, spirals, grinding and shaking tables, followed by standard tin dressing techniques including finer grinding and sulphide flotation, it has been demonstrated that 55-58% of the total tin is recovered into a plus 56% Sn, low impurity tin concentrate. An additional 5-6% recovery is possible from a fine tin circuit.
Due to the simplicity of the coarse tin only circuit, this processing flow sheet has now been chosen as the most viable option for the DFS, with the possible addition of a fine tin recovery circuit and/or supplementary crushing options being investigated as part of future optimisation work to further increase recovery rates. Ongoing recovery studies on lower-grade samples are also currently in progress, designed to obtain a good grade-recovery curve for use in the DFS, which we aim to complete during Q1 2024. These results will be announced when received.
Summary
Based on the results of this test work, a simple processing facility has been designed consisting of (Figure 1):
Figure 1 shows the current simplified flowchart for the proposed mill design.
First Tin CEO Thomas Buenger said: “This processing testwork has identified a clear path forward to produce a saleable tin concentrate from the Taronga tin deposit using very simple, cheap, off the shelf mineral processing equipment such as jigs, spirals and shaking tables. A good quality concentrate can be produced at reasonable recovery rates using very simple equipment, resulting in lower capital and operating costs.
“These results also show that recoveries can be boosted by recovering tin from the fine fraction (<38µm) using more complex and sophisticated high G force gravity separation techniques as well as via cassiterite flotation. We look forward to announcing further optimisations at this asset in the coming months.”
The project is owned by First Tin’s 100% owned Australian subsidiary, Taronga Mines Pty Ltd (“TMPL”).
Enquiries:
First Tin
Via SEC Newgate below
Thomas Buenger – Chief Executive Officer
Arlington Group Asset Management Limited (Financial Advisor and Joint Broker)
Simon Catt 020 7389 5016
WH Ireland Limited (Joint Broker)
Harry Ansell 020 7220 1670
SEC Newgate (Financial Communications)
Elisabeth Cowell / Molly Gretton
Notes to Editors
First Tin is an ethical, reliable, and sustainable tin production company led by a team of renowned tin specialists. The Company is focused on becoming a tin supplier in conflict-free, low political risk jurisdictions through the rapid development of high value, low capex tin assets in Germany and Australia.
Tin is a critical metal, vital in any plan to decarbonise and electrify the world, yet Europe has very little supply. Rising demand, together with shortages, is expected to lead tin to experience sustained deficit markets for the foreseeable future. Its assets have been de-risked significantly, with extensive work undertaken to date.
First Tin’s goal is to use best-in-class environmental standards to bring two tin mines into production in three years, providing provenance of supply to support the current global clean energy and technological revolutions.
Swiss Resource Capital AG
Poststrasse 1
CH9100 Herisau
Telefon: +41 (71) 354-8501
Telefax: +41 (71) 560-4271
http://www.resource-capital.ch