Polyethylene (PE) / Polyamide (PA) multilayer films are mechanically recyclable!
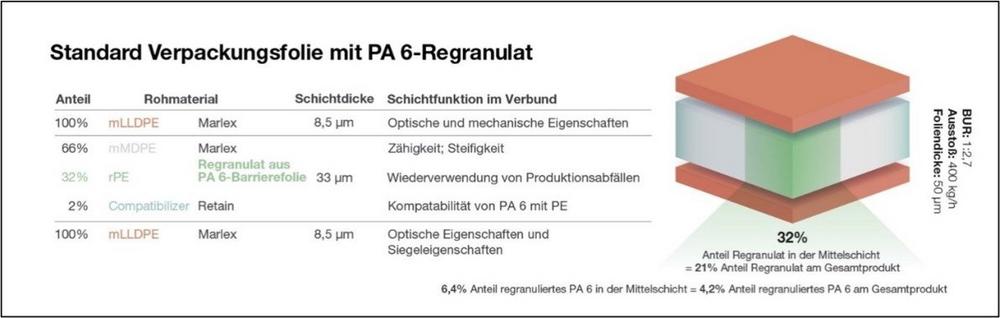
Breaking News:
Die Macht der Stimme – Erfolgreich kommunizieren im Beruf und Alltag
Mit Frequenzumrichtern zur Höchstleistung: Effizienz und Flexibilität neu definiert
Effizienz neu gedacht: IE3- und IE4-Motoren für maximale Energieeinsparung
Wenn Japan Ihr Markt ist: Wie Jp-Domains Ihren Erfolg sichern
Feierliche Eröffnung des Agri-Solarparks Löffingen – Cem Özdemir würdigt zukunftsweisendes Projekt
Kathmandu Nepal
Sonntag, Nov 24, 2024
Authors: Rolf-Egbert Grützner*; Berthold Moorkamp**, Hans-Udo Beckmann**
The authors advocate for a fact-based assessment, and these assertions, which are not covered by the state of science, are not comprehensible. In the 2022 edition of the minimum standard of the Central Packaging Register in Germany[#15]., the DfR regulations were adapted to the facts and co-extruded PE/PA multilayer films with a defined coupling agent/polyamide ratio were accepted as compatible components in the PE film stream.
The production of high-quality PE/PA/EVOH regranulate containing blown films on an industrial scale was presented for the first time during the house fair (Expo) of engineering company Windmöller & Hölscher (W&H), which was held in parallel with the 2022 plastics exhibition “K”. The optical and mechanical performance of these regranulate containing blown films proved comparable to virgin material.
In detail, the presentation was made by producing 3-layer films, each with a total thickness of 50 µm on a VAREX II air-cooled blown film line with a blow-up ratio (BUR) of 1:2.7 and a throughput of 400kg/h. The middle layers of the films produced contained 25 – 32 wt% regranulates.
Figure 1 summarizes the details of the integrated PE/PA6 regranulate (based on a primary film structure with 20% PA6 = Ultramid® B40LN), Figure 2 illustrates the same information for the 3-layer film with PE/CoPA/EVOH regranulate (based on a primary film with 25% PA6/6.6 CoPA = Ultramid® C40LN and 3% EVOH).
All details of the primary films used, or their structures can be tracked in[#16].
Figure 3 gives a representative visual impression of the optical quality of Film 1 (containing PE/PA6 regranulate), and tables 4 and 5 summarize the key mechanical and optical properties of the 3 films investigated. The data are displayed in comparison to the reference film made of 100% polyethylene.
The mechanical properties from the tensile test are summarized in figure 4 and quantify very small differences between the pure PE reference (blue) and the two PA-containing film formulations. Both PE/PA6 or PE/CoPA/EVOH regranulate containing film show comparable values (tensile strength) or even slightly improved parameters (elongation at break) or a plasticizer effect of max. approx. 10% (reduction of tensile modulus) in the longitudinal direction of the measured films. While the lower values of tensile strength and elongation at break are found in the transverse direction with < 6% loss, the differences in the tensile modulus with max. < 10% also fall safely within an acceptable range.
Figure 5 shows significant improvements in the tear propagation resistance (Elmendorf) in the longitudinal and transverse directions (higher values of the orange (PE/PA6 regranulate) and gray (PE/CoPA/EVOH regranulate) bars, respectively, compared to the PE reference shown in blue). In addition, all 3 film variants showed comparable measured values for puncture resistance as well as haze = transparency.
In contrast to the recycling of mixed “post-consumer”packaging waste, the optical performance of a film containing regranulate plays a significant role for an effective recycling concept for the incorporation of “post-industrial”film waste, in addition to processability and mechanical properties. A cloudy film with small blemishes (specks) is not accepted in practice.
For this reason and the mechanical and optical characteristics of the finished film, the optical quality during production was assessed in the form of an on-line optical analysis of visible and measurable defects on the film surface (for example impurities (“black spots”) or specks).
Figure 6 below shows representative sections of the gel levels recorded during film production for the pure PE reference film and the complex variant with the addition of PE/CoPA/EVOH regranulate, classified according to the diameter of the defects in
µm = f(time).
Figure 6 shows that the film variant using PE/CoPA/EVOH regranulate exhibits a significantly reduced level for the “smaller” gel diameters of </= 300µm (red line) as well as </= 500µm (blue line) compared to the PE reference, while additional gel diameters of > 1000µm occur more than the PE reference, but still at a very low level.
It was shown that excellent quality levels can be achieved when incorporating PE/PA blended regranulates into new PE-based film structures, even with concentrations of > 5% PA and when using PA/EVOH combinations.
The regranulated film’s mechanical and optical properties convincingly confirm the practical feasibility of a “0% waste strategy” of internal PE/PA6 or PE/CoPA/EVOH processing waste during production. They also provide further confirmation of the compatibility of PA-containing multilayer film structures in the PE waste stream as a basis for acceptance of such multilayer composites in packaging applications with proven recyclability. Thus, nothing stands in the way of using the known advantages of polyamides in terms of barrier effect and mechanical strength to protect the packaged goods and reduce packaging volume for overall sustainable packaging solutions.
Furthermore, the results presented here demonstrate and confirm the compatibility of PE/PA/EVOH multilayer composite films in the PE waste stream from mixed flexible household plastic waste. Since the polyamide content in the waste mixture is in the low single-digit percentage range, it does not pose any risk to the recyclability of the packaging.
References
[#1] https://www.cyclos-htp.de/…
[#2] 2020-PO-011-UBE-technology-approval-letter.pdf (recyclass.eu).
[#3] 2021-PO-016-Umaras-technology-approval-letter.pdf (recyclass.eu).
[#4] https://ube.es/…*ci2o9i*_up*MQ..*_ga*NzE0MjY1NjUwLjE2NzYzMTIyOTA.*_ga_WMMW6C900D*MTY3NjMxMjI4OS4xLjEuMTY3NjMxMjMzNi4wLjAuMA..
[#5] Certificate 2548-2021-002684 Bogucki film multilayer PE-PA; cyclos-HTP, 2021
[#6] Certificate 2141-2022-003085 VF Packaging_AMILEN; cyclos-HTP, 2022
[#7] https://packaging-journal.de/… 12/2022, Allflex SR, Allvac Folien GmbH
[#8] Certificate 2506-2021-002622 Parnaplast Industria de Plasticos Multilayer PE-PA; cyclos-HTP, 2021
[#9] Joint presentation BASF SE – Ube: Recycling of Multilayer films containing Polyamide; General Summit CEFLEX, 03_2021
[#10] Grützner, R.-E.; Bothor, R.: Coextruded PE/PA multilayer films are recyclable! www.cyclos-htp.de/…
[#11] Pacitti, St.: Complex approach, Plastics in Packaging PIP, 03_2021, 25
[#12] Grützner, R.-E.; Mechanical recycling of PE/PA6 – multilayer composite films, Webinar BASF SE – ZLV Kempten, 12_2020.
[#13] Design for Recycling Guidelines – RecyClass
[#14] https://guidelines.ceflex.eu
[#15] Minimum standard for assessing the recyclability of packaging subject to system participation pursuant to §21 (3) VerPackG, Zentrale Stelle Verpackungsregister, Edition 09/2022
[#16] OnePager: "PE – film with PA-recyclate" Windmöller & Hölscher Expo, Lengerich 10/2022
* BASF SE, 67056 Ludwigshafen, Germany; ** Windmöller & Hölscher, 49525 Lengerich, Germany
Windmöller & Hölscher KG
Münsterstr. 50
49525 Lengerich
Telefon: +49 (5481) 14-0
Telefax: +49 (5481) 14-2649
http://www.wuh-lengerich.de