Powerful and efficient: solid carbide tools in metal-working
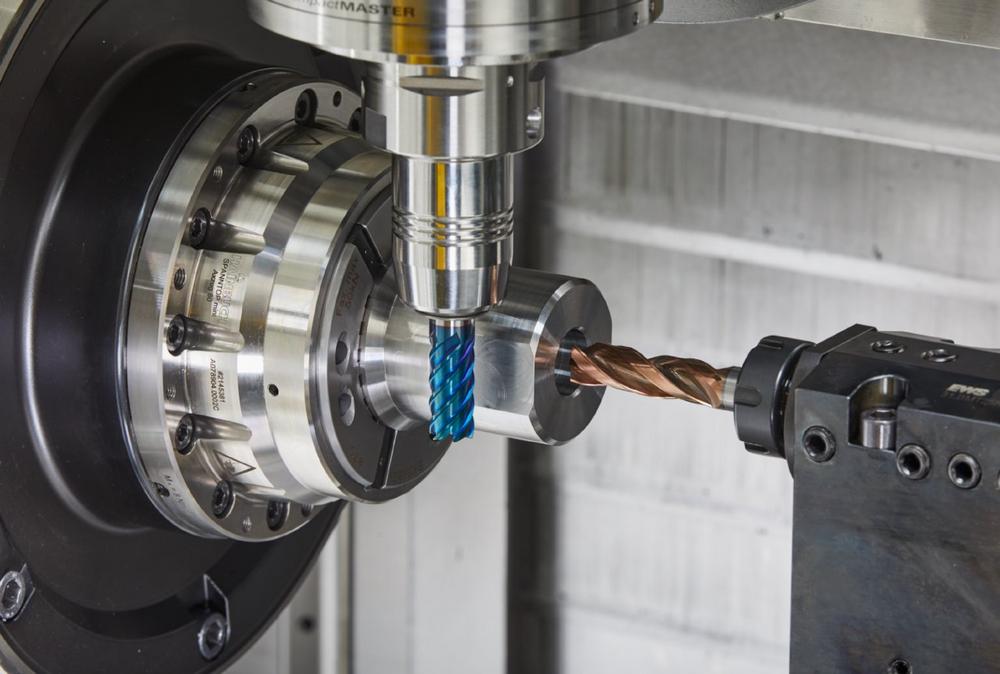
Breaking News:
Bioplastik im Test: Wie funktioniert der biologische Abbau wirklich?
revolt Universal-Reiseadapter & Notebook-Netzteil UTA-100, GaN, 4xUSB-C, 1xUSB-A, PD
Mitarbeitende in Sozialeinrichtungen – neue Potentiale durch die Triple-Win-Strategie
Christa erhält Prokura und ist neuer Hauptabteilungsleiter bei der uniVersa
Relaunch von CAPDL: Koalition für amerikanische Diplomatie hat sich neu aufgestellt
Kathmandu Nepal
Donnerstag, Jan. 16, 2025
The efficiency of solid carbide tools has long been proven. Their wear resistance and the consistent quality of machining results are impressive for producing large batches. This allows users to quickly achieve economic results in their production and they outweigh the higher prices of the tools. Nevertheless, production managers should not blindly rely on solid carbide tools in the hope of having a universal all-round tool. This is because developments in solid carbide technology mean that it is now possible to produce a wide range of tools for different purposes.
Many details are important for solid carbide tools
Once you select the right material with the right coating, the expertise of the tool manufacturer then has a decisive impact on the quality of the tool. For example, a supplier must know exactly what grain and which grinding finish are the right ones to use with steel, hardened steel, cast material, aluminium, non-ferrous metals or exotic materials such as titanium, Inconel or Hastelloy. Other factors to consider are whether the process requires roughing, finishing, dry or wet machining, HSC machining, what are the cutting depths, the helical pitch, and so on.
With so many vital details, it quickly becomes obvious that there is no such thing as a universal all-round tool for all processes and materials. Trustworthy suppliers should therefore offer a wide range of products. Arno Werkzeuge from Ostfildern is a supplier that takes this complexity in production together with the plethora of possibilities very seriously. They have extensive knowledge of materials, numerous applications and enormous expertise. The family-owned company offers a wide range of solid carbide tools for a variety of applications as well as specific requirements.
Suppliers with a wealth of experience and a wide product range have the leading edge
"Thanks to the relationships we have built up with our customers over many years, we have amassed a large pool of application knowledge. This is why our expertise allows us to offer exactly the right solid carbide tools for a wide range of machining processes and materials," says Product Manager Marco Staiger from Arno Werkzeuge. You realise this straight away when you browse through the 400-page catalogue of solid carbide milling cutters, drills and thread-milling tools. But if you are then put off in your search for the right tool, Staiger reassures you by emphasising: "Our application consultants will help you select the right solid carbide tools quickly and competently."
And of course, the range also includes tools for general applications that cover a specific universal range. For many users, the Arno-FP milling cutter is an ideal entry-level tool that covers a wide range of metal-cutting operations on steel, stainless steel and cast materials. The universal milling cutter made of powder metal HSS steel is TiAIN-coated, extremely tough and wear-resistant. This ensures a longer tool life and maximum cutting performance. The AF solid carbide milling cutter is also suitable for general machining applications including steel and cast materials. It is just as suitable for wet and dry machining as it is for conventional or high-speed milling.
Experienced consultants help you find the right tool
If the application is even more specialised, the consultants can fall back on a further nine special milling cutters which can be used to their full potential depending on the machining process and the material. For example, AFA milling cutters offer excellent results with soft cuts in aluminium alloys. When it comes to steels, cast iron and stainless steels, there is a group of three special high-performance tools. If you machine exotic materials such as titanium or stainless steels such as nickel alloys at high cutting speeds, there are two milling cutters available: the AFE and the AFJ. And finally, users will find the right milling cutters for high-speed machining and dry cutting in the top league of pre-hardened steels up to HRC 55 and extremely hardened steels up to HRC 70.
Even when drilling, users come up against many machining process requirements, quite apart from the numerous materials, such as stainless steels, extremely hardened steels, carbon steels, cast iron, aluminium or aluminium alloys. If deep holes need to be drilled or if the feed rate must be as high as possible, can a universal drill be used or should chamfering be centred? Metal-cutting companies can also choose from drills with or without through tool cooling.
Special tools for the dry machining of aluminium
Customers appreciate the diversity of the range of solid carbide tools from Arno Werkzeuge. Not only that. Many customers recognise they can achieve tight tolerances using the fully ground, high-precision tools. They are also extremely sturdy and sharp. Here, Staiger says, "Our product range also has tools to machine very small workpieces or to cater for special requirements." They achieve results that are impossible with cutting inserts. For example, a user who machines tubes for food technology gets the best results using a soft-cutting but extremely sturdy tool.
Conclusion:
Versatile, precise and powerful: solid carbide tools increase efficiency and precision in metal-cutting operations
Solid carbide tools have their undisputed strengths. When they are customised for use with specific machining processes and materials, they greatly enhance production efficiency and precision. When a supplier also offers competent advice, a wide range of products and can supply tools customised to specific requirements, it could be the right partner. If the price is also interesting, nothing will stand in the way of efficient metal-cutting using solid carbide tools.
Customer proximity and development power: Emil Arnold set up ARNO Werkzeuge Karl-Heinz Arnold GmbH in 1941 as an innovative tool manufacturer and the company is now in the third and fourth generations of owner management. The company has a high manufacturing depth, in-house development competence and a global sales organisation. It produces highly modern, high-performance tools which are used world-wide in production with fixed headstock machining, Swiss type machining, parting, grooving, turning, drilling and milling. One of the company specialities is ground high-positive indexable inserts for complex manufacturing operations. Here, ARNO offers the largest portfolio in the world.
Customised tool solutions, which later become highly coveted standards, are developed in close collaboration with our customers, taking their requirements into consideration. The tradition-based company ensures customer proximity by a work force of over 200 employees at its head offices in Ostfildern and its numerous sales offices all over the world. ARNO last achieved a turnover of around €56 million, almost back to pre-crisis levels.
Info box: solid carbide tools
Many details are important for solid carbide tools: Developments in carbide technology mean that a wide range of very different tools can now be manufactured. Depending on the grain size of the tungsten carbide. which is the grade in predominant use. combined with a binder, the cutting tools created today can be specifically adapted to a wide variety of processes and materials.
Nowadays, the average grain size of tungsten carbide ranges from 20 µm to less than 0.5 µm. Consequently, the grain used for sintering processes in tool production is categorised into coarse grain, normal grain, ultrafine grain and ultrafine grain. The finer the grain, the harder and more resistant the tool. Contrary to previous expectations, there is also a significance increase in bending strength. In addition, thermal conductivity is reduced and this is a decisive factor for a long tool life.
ARNO Werkzeuge
Karlsbader Straße 4
73760 Ostfildern
Telefon: +49 (711) 34802-0
Telefax: +49 (711) 34802-130
http://www.arno.de